


Your Journey. Your Success. Your Story.
Lean in management and manufacturing
Lean is about eliminating waste
Summing up the intent of Lean
"creating effectiveness and efficiency within a value stream through the elimination of waste"
A culture of leading producers and manufacturers
Lean and Six Sigma have proven to be effective time and time again, which is why the philosophy continue to be a staple in the company culture of many leading production and manufacturing companies.
Common stages of creating excellence with Lean
Simple cycle remarkable value creation
5 simple stages in the cycle with remarkable value creation.

What is Lean?
Lean is a highly effective methodology that aims to eliminate waste from an organization's supply chain, value chain, processes and workflow. By identifying what is value within the organization and how it flows, Lean helps to streamline processes and improve efficiency. Businesses and organizations adopting lean are innovative and benefit from improved productivity, reduced costs, and ultimately, greater customer satisfaction.
Is it worth the journey?
Exciting challenging and full of humps and bumps maybe?
Like all journeys to create organizational culture and excellence it isn't without its complexities, technicalities and challenges. It is an incredibly rewarding journey there will be humps and bumps on the way and in the end you won't look back but forward with assurance and confidence.
Sharing a thought
What could you achieve with an organizationally integrated and functionally synergetic teams, systems, processes and workflows that are effective and efficient mean to you?
What is your next step towards organizational excellence?
We can get deep in it with your journey
We are about real change and improvement creating real excellence that is resilient and sustainable because it’s challenging and for us seeing you succeed is incredibly rewarding.
Scroll on to discover more
Developing maintenance management excellence can be an exciting journey for an organization in creating an unfair advantage.
Six Sigma in management and manufacturing
Six Sigma is about controlling variation
What is Six Sigma?
Six Sigma is a methodology that uses statistical mathematics to solve problems with capability and variation within a process. It is also used to determine the interacting factors to produce the best outcome or tolerancing and more. There are other Six Sigma uses too such as product or technology innovation and organizational culture change.
Summing up the intent of Six Sigma
"creating effectiveness and efficiency within a process through the control of variation"
A culture of leading producers and manufacturers
Lean and Six Sigma methods have proven to be effective time and time again, which is why the philosophy continue to be a staple in the company culture of many leading production and manufacturing companies.
Six Sigma DMAIC Process
The DMAIC Process
Within Six Sigma the DMAIC Process is the most common but there are others depending on the intent and context.
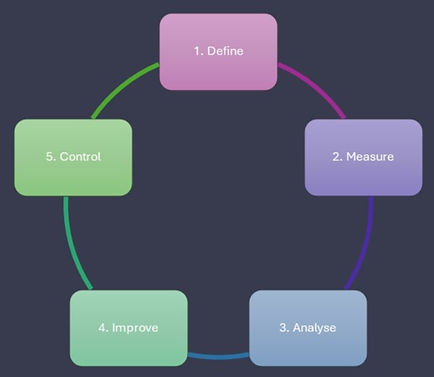
Product and Technology innovation with DMADV
The DMADV Process
Though less common and has its specific application in innovative Product and Technology development is DMADV. The method can be useful in the creation of innovation from concept to prototype and it is an advance topic in the Six Sigma library.

Design For Six Sigma (DFSS) the rare offspring
What is Design For Six Sigma?
Design For Six Sigma is all about releasing products out into the wild consumer jungle with very little defects or a minimum sigma level of 4.5. This means that it is 99.38% defect free. Holy moly imagine that makes the hairs on your arms stand up.
Lean Six Sigma versus...
Truths and myths about Lean Six Sigma
Agile is better
Agile has its place specifically in software development where there are no clear answers. Though the only negative thing we need to say about Agile is that you need to have a dedicated Agile team that is familiar with the Agile process, team roles, and responsibilities. This is sadly an overhead for many organizations and recently the methodology has been erroneously applied causing organizational performance problems.
ADKAR is better
ADKAR compliments Lean and uses qualitative methodologies to remove the barriers and help individuals understand and overcome the barriers of change through its 5 foundations of Awareness, Desire, Knowledge, Ability and Reinforcement. It is a modern methodology and rooted in Organizational Behavior and Psychology. The methodology systematic guides individuals within an organization through the process of change and it is easy to use and understand. Qualitative methods are the emotional aspects of change.
Its a toe cutting exercise
Why cut off healthy toes if its not gangrenous or needing to be cut off? Lean is about eliminating waste and value creation. Sure there may be some negative side effects because of accumulated bloat before changing organizational mindset but in no way is Lean about whittling it down to the point where your business is no longer functioning or capable. If you get there, mate, something is wrong and you need to give us a call ASAP.
Agile versus Lean the time wasting debate on semantics and principle of approach. Both are good in their respective application
More on Agile versus Lean debate
Agile methodology was developed in response faced by software companies in meeting customer requirements while minimizing costs. It emerged during the modern age of software engineering as a solution to the problem of wasted resources in producing SaaS products that failed to meet customer needs. The intent of Agile is to build a Minimum Viable Product that can be quickly deployed, iterated and scaled through consumer feedback while recovering the initial development costs. We feel Agile is excellent in SaaS products and Technology products because of its iterative nature and how it integrates with the principles of product engineering, product development and product management lifecycle but has fundamental problems when used as an organizational change management technique.
ADKAR and Lean just goes hand in glove contrary to popular belief. Its not a debate or an argument.
More on ADKAR versus Lean
Both are excellent methodologies for change and have their respective strengths. ADKAR uses qualitative methodologies to remove the barriers and help individuals understand change through its 5 foundations of Awareness, Desire, Knowledge, Ability and Reinforcement. It is a modern methodology and rooted in Organizational Behavior and Psychology.
​
​
Lean Six Sigma is deeply rooted in Engineering, Mathematics, Business and Economics. Lean Six Sigma uses both qualitative and quantitative methodologies to enable organizational change and improvement. Lean does this through the tools within the methodology that is aimed at removing waste from an organizations value stream and Six Sigma does this through removing variations from an organizations process. It has many applications from Business Process Management through to the engineering, manufacturing and production shop floor. Quantitative methods are fact based aspects of change and has a heavy reliance on data.
​
At Gaishan we use both ADKAR and Lean Six Sigma methods because we believe in holistic organizational change that benefits everyone within the organization. You can expect that we are able to guide you through the technicalities and complexities of change that is flexible, adaptable, lean and agile with the right advisory and consultation to suit your needs with high adoption.

How can Lean Six Sigma benefit you?
Here are some examples
-
Business strategic alignment
-
Business process alignment
-
Consistent processes and workflow
-
Control over process and workflow
-
Data driven decision making
-
Enhanced business growth
-
Enhanced financial performance
-
Enhanced OEE
-
Enhanced organizational reputation
-
Improved customer satisfaction
-
Improved operational performance
-
Improved organizational capability
-
Improved process accountability
-
Improved process responsibility
-
Improved profit margin
-
Improved quality performance
More examples?
-
Improved risk management
-
Informed decision making
-
Innovation
-
Integrated organizational functions
-
Internal knowledge and experience
-
Organizational culture
-
Organizational resilience
-
Organizational sustainability
-
Predictable outcomes
-
Process and workflow stability
-
Process and workflow waste reduction
-
Reduce defects and rework
-
Shareholder confidence growth
-
Stakeholder confidence growth
-
Utilized talent